Hello all,
Just want to follow up with this post I started with some new (and very interesting findings) of the motor. If you forgot what the discussion was about, please see highlighted blue text below. We did conclude at the time that the motor had some internal problems--we pulled the questionable motor and sent it to the local shop and installed a spare, and the spare has been running without any issues.
Today, we got the chance to visit the motor shop and witnessed some tests on this motor. Observations are interesting. Insulation check did not pick up anything obvious (which is consistent with our initial finding during field troubleshooting). The motor shop just cleaned the motor and varnished and baked it, and after this the motor is able to run on both low and high speeds. Everything seems to be alright except for the following observations
No-load run on low-speed currents: 91, 90, 91 (low speed FLA is 161), test voltage 480V
No-load run on low-speed currents: 189, 186, 189 (hi speed FLA is 225), test voltage 480V
and PdMA test shows some imbalance on winding resistance and inductance
We just don't really know what causes this motor to pull higher-than-anticipated currents at the moment. We have an almost identical motor, and during no-load run, its low/hi-speed currents are 65/145, so we were hoping to see approximate the same on this motor.
I'm simply still scratching my head at the moment, any thoughts on what could be going on with this motor? Also, what could be a possible explanation on why the motor kept tripping on hi-speed (solo no-load run) in the field while no obvious faults were found in this motor during shop inspection?
Post couple weeks ago:
Recently, I've had a two-speed motor tripping motor feeder breaker (instantly) on high speed only.
First off, shown below are the motor specs
low speed: 480V, 100HP, FLA = 161amps, SF=1.0
high speed: 480V, 200HP, FLA = 225amps, SF=1.0
Motor starter is using a three contactor configuration: one for low speed, and one for high speed, and the third contactor is used to bring leads T1, T2, and T3 together during high-speed operation.
Normal opeartion use: blower
Operation procedure: start motor at low-speed first; after motor speed is established (and process conditions satisfied), hit "stop" button and then hit fast-speed start button to bring the motor to hi-speed.
Now, back to the question and how we troubleshoot: We disconnected the motor at the service head, and then energized the feeder and tried both low and hi speed, breaker did not trip. So we eliminated the potential problem of a feeder fault; then we de-coupled the motor from load and connected the leads back to the motor and solo run the motor-----it turned out that low speed is running fine, but as soong as we switch to hi-speed, it trips, and this is the same symptom with the motor having load on.
Interesting thing that we observed was that, during solo motor run, the motor was already pulling 175amps on all three phases,while its FLA for low-speed is 161.
We suspect that the motor is bad and possibly has a internal winding fault, however insulation resistance test didn't show any obvious results--we megged all six leads of the motor to ground, but each lead is reading above 6 Mohms.
So my question is, what could possiblly cause the trip? What kinda of internal motor internal fault could cause the motor to operate on low-speed only but not on hi-speed?
Just want to follow up with this post I started with some new (and very interesting findings) of the motor. If you forgot what the discussion was about, please see highlighted blue text below. We did conclude at the time that the motor had some internal problems--we pulled the questionable motor and sent it to the local shop and installed a spare, and the spare has been running without any issues.
Today, we got the chance to visit the motor shop and witnessed some tests on this motor. Observations are interesting. Insulation check did not pick up anything obvious (which is consistent with our initial finding during field troubleshooting). The motor shop just cleaned the motor and varnished and baked it, and after this the motor is able to run on both low and high speeds. Everything seems to be alright except for the following observations
No-load run on low-speed currents: 91, 90, 91 (low speed FLA is 161), test voltage 480V
No-load run on low-speed currents: 189, 186, 189 (hi speed FLA is 225), test voltage 480V
and PdMA test shows some imbalance on winding resistance and inductance
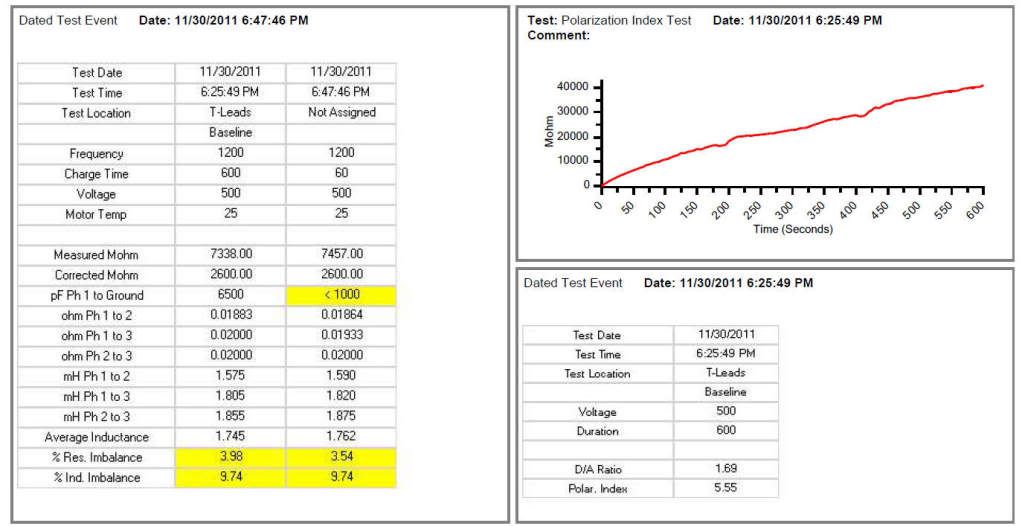
We just don't really know what causes this motor to pull higher-than-anticipated currents at the moment. We have an almost identical motor, and during no-load run, its low/hi-speed currents are 65/145, so we were hoping to see approximate the same on this motor.
I'm simply still scratching my head at the moment, any thoughts on what could be going on with this motor? Also, what could be a possible explanation on why the motor kept tripping on hi-speed (solo no-load run) in the field while no obvious faults were found in this motor during shop inspection?
Post couple weeks ago:
Recently, I've had a two-speed motor tripping motor feeder breaker (instantly) on high speed only.
First off, shown below are the motor specs
low speed: 480V, 100HP, FLA = 161amps, SF=1.0
high speed: 480V, 200HP, FLA = 225amps, SF=1.0
Motor starter is using a three contactor configuration: one for low speed, and one for high speed, and the third contactor is used to bring leads T1, T2, and T3 together during high-speed operation.
Normal opeartion use: blower
Operation procedure: start motor at low-speed first; after motor speed is established (and process conditions satisfied), hit "stop" button and then hit fast-speed start button to bring the motor to hi-speed.
Now, back to the question and how we troubleshoot: We disconnected the motor at the service head, and then energized the feeder and tried both low and hi speed, breaker did not trip. So we eliminated the potential problem of a feeder fault; then we de-coupled the motor from load and connected the leads back to the motor and solo run the motor-----it turned out that low speed is running fine, but as soong as we switch to hi-speed, it trips, and this is the same symptom with the motor having load on.
Interesting thing that we observed was that, during solo motor run, the motor was already pulling 175amps on all three phases,while its FLA for low-speed is 161.
We suspect that the motor is bad and possibly has a internal winding fault, however insulation resistance test didn't show any obvious results--we megged all six leads of the motor to ground, but each lead is reading above 6 Mohms.
So my question is, what could possiblly cause the trip? What kinda of internal motor internal fault could cause the motor to operate on low-speed only but not on hi-speed?
Last edited: