drbond24
Senior Member
- Location
- Barboursville, West Virginia
I have what I believe is an induced voltage problem. I have this simple circuit:
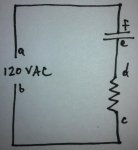
The contact between e and f is a control system relay output that is rated for 220 VAC and has been verified to operate properly.
The coil between c and d is a 120 VAC operated contact in a valve positioner control cabinet. Anything greater than 22 VAC is sufficient to energize it, thereby opening the corresponding valve. Anything less than 8 VAC is de-energized which closes the valve. The area between 8 and 22 VAC is designated 'undefined' by the instruction manual, which I'm guessing means it could go either way.
The a side of the 120 VAC is the line and the b side is the neutral.
Now, when the contact is closed I have 120 VAC on the coil and the valve opens. No problem. However, when the contact is open I have 50 VAC on the coil which keeps the valve open. This 50 VAC manifests itself on the d side of the coil (referenced to ground). The voltage on the other side of the coil, using the same reference, is less than 1 VAC. We checked the contact and it is working. This voltage 'appears' on the conductor between e and d.
The problem, I think, is in the cable run between the 120 VAC and the contact. I can lift the wires completely on both ends and still measure 50 VAC on the cable. I did this with a Fluke 87V. I doubt this voltage has much 'umph' to it, but it is enough to keep the coil energized which, per the manual, requires 1.8 mA.
I cannot access the wire pull between these two points, but I know that it is in a cable vault with countless other cables. It is probably inside a large conduit with a bunch of other cables with various purposes. The cable is a shielded 3 conductor 16 AWG. The shield is grounded on one end.
My preferred solution at this point would be to put something across the coil terminals to counteract this voltage if that is possible, but I do not know what to use. I suspect an RC device but I have no idea how to go about sizing R or C. Other than pulling new wire via a different route, what can I do to remove or counteract this 50 VAC?
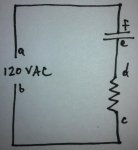
The contact between e and f is a control system relay output that is rated for 220 VAC and has been verified to operate properly.
The coil between c and d is a 120 VAC operated contact in a valve positioner control cabinet. Anything greater than 22 VAC is sufficient to energize it, thereby opening the corresponding valve. Anything less than 8 VAC is de-energized which closes the valve. The area between 8 and 22 VAC is designated 'undefined' by the instruction manual, which I'm guessing means it could go either way.
The a side of the 120 VAC is the line and the b side is the neutral.
Now, when the contact is closed I have 120 VAC on the coil and the valve opens. No problem. However, when the contact is open I have 50 VAC on the coil which keeps the valve open. This 50 VAC manifests itself on the d side of the coil (referenced to ground). The voltage on the other side of the coil, using the same reference, is less than 1 VAC. We checked the contact and it is working. This voltage 'appears' on the conductor between e and d.
The problem, I think, is in the cable run between the 120 VAC and the contact. I can lift the wires completely on both ends and still measure 50 VAC on the cable. I did this with a Fluke 87V. I doubt this voltage has much 'umph' to it, but it is enough to keep the coil energized which, per the manual, requires 1.8 mA.
I cannot access the wire pull between these two points, but I know that it is in a cable vault with countless other cables. It is probably inside a large conduit with a bunch of other cables with various purposes. The cable is a shielded 3 conductor 16 AWG. The shield is grounded on one end.
My preferred solution at this point would be to put something across the coil terminals to counteract this voltage if that is possible, but I do not know what to use. I suspect an RC device but I have no idea how to go about sizing R or C. Other than pulling new wire via a different route, what can I do to remove or counteract this 50 VAC?
Last edited: