Final solution for malfunction detection and maintenance
Final solution for malfunction detection and maintenance
Sorry for not giving too many details.
The 37kw on-grid pv system will be installed in front of our building as showcase.
We will use the new Leonics 3phase multistring inverters (2x15kw)
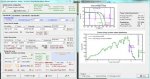
We are about to introduce in our portfolio energy optimization and management systems. It comprises many power meters distributed along the building, sending data to a micro-controller by wifi. We want to track and manage energy sources (pv system, grid, biogas generators) and loads.
The microcontroller will be linked (RS485) to the inverter as well, so once we have the system I think it would be a good idea to track the performance of the modules (field sensors plus Perez-Ineichen algorithm ) and also detect any kind of malfunction.
Following your indications, lets see if i can come up with a good solution (excuse my ignorance):
TRACKING. Worst months (November, December, January) from 10:30 to 11:30, the rest of the year from 12:00 to 13:00
-(1) Performance: Pyranometer + temperature sensors + Perez algorithm---> Error>Tolerance ---> ALARM
-(2) Strings current tracking: currents between 10-22% of each other everything OK ----> current difference bigger than 30% ----> ALARM
-(3) Array Wh harvesting: real time data from inverter ----> Array harvesting drop 50% ---> ALARM
Would it be better to track (2) and (3)? or just (3) is enough?
Once we detect a malfunction how do we find the wrong module? Thermographic camera, visual inspection and V/I measurement of each module?
MAINTENANCE:
- Cleaning modules every month
- Visual inspection, connections and corrosion every 6 months?
- Thermographic camera every 6 months or only when we detect a fault?
- Should we check open diodes by generating shadow (current near 0A) for example once a year?
Thanks for your help