brycenesbitt
Senior Member
- Location
- United States
I'm looking for some help with NEC code interpretation wiring associated with EV charging.
This is for a series of "Wallbox" brand EVSE chargers which have an RS-485 control circuit.
In short they measure the current at the main using CT clamps, and then throttle the vehicle's charging rate to moderate peaks.
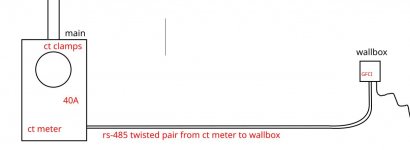
The question is where to run the control wires. The two options are:
Wallbox is an Intenational company, and they assume for Europe presumably that all the wiring will happen in the same conduit.
I'd prefer to keep all the wiring in the same enclosure as it's neater, cleaner, cheaper. In my view it's less subject to future damage if integral.
I'm not so sure I can make that fly under the NEC. These wires are clearly "functionally associated"
I see:
Q. I’m working on an electric gate installation. Can I install control wiring in the same raceway with electrical power conductors?
Mike Holt's A: Maybe. According to 725.26(B)(1), Class 1 circuits can be placed in the same cable, enclosure, or raceway with power-supply circuits, if the equipment powered is functionally.
Install location is California, which will switch soon to the 2022 NEC. I can readily source appropriate 600V rated twisted pair wire with shield and 600V sheath.
The control wire is NOT separate from the 240V wiring inside the Wallbox:
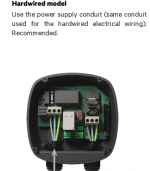
Your thoughts on what it takes to make this work safely and satisfy most AJH's?
Can I place a foam sleeve on standard RS-485 twisted pair cable to meet the 1/4" separation requirement for example?
This is for a series of "Wallbox" brand EVSE chargers which have an RS-485 control circuit.
In short they measure the current at the main using CT clamps, and then throttle the vehicle's charging rate to moderate peaks.
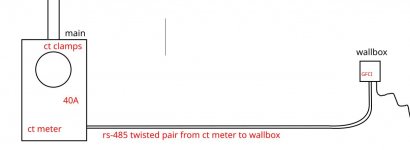
The question is where to run the control wires. The two options are:
- Place the CT clamps on the service entrance cable. Create a separate box and conduit channel.
Drill a hole in the main panel to run the CT clamp sense wires out.
Thus the low voltage CT clamp wires will exit the main panel as quickly as possible, then rejoin the power supply cables at the Wallbox.
- Run everything within the same enclosure and conduit. The ct meter DIN rail mounted and requires the low voltage CT sense wires, and access to 240V power.
Wallbox is an Intenational company, and they assume for Europe presumably that all the wiring will happen in the same conduit.
I'd prefer to keep all the wiring in the same enclosure as it's neater, cleaner, cheaper. In my view it's less subject to future damage if integral.
I'm not so sure I can make that fly under the NEC. These wires are clearly "functionally associated"
I see:
Q. I’m working on an electric gate installation. Can I install control wiring in the same raceway with electrical power conductors?
Mike Holt's A: Maybe. According to 725.26(B)(1), Class 1 circuits can be placed in the same cable, enclosure, or raceway with power-supply circuits, if the equipment powered is functionally.
Install location is California, which will switch soon to the 2022 NEC. I can readily source appropriate 600V rated twisted pair wire with shield and 600V sheath.
The control wire is NOT separate from the 240V wiring inside the Wallbox:
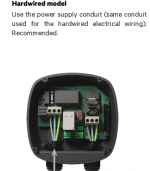
Your thoughts on what it takes to make this work safely and satisfy most AJH's?
Can I place a foam sleeve on standard RS-485 twisted pair cable to meet the 1/4" separation requirement for example?