KP2
Senior Member
- Location
- New Milford, CT
Hello, I am looking into replacing an old air compressor motor with a new energy efficient motor and I have some confusion on how to obtain the Brake Horsepower rating, (BHP).
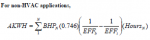
Reminder:
N = The total number of defined combinations of load and Hours. (e.g., 1=10% of the hours at 100% load; 2=20% of
the hours at 83% load, etc.)
BHPN = the HP required by the load at combination N
hoursN=the time, in hours, that is spent at combination N
I have this formula, BHP = E x √3 x I x Percent Efficiency x PF/746, but the utility reminder is confusing me, and when I research the BHP it is refered to the demand of the compressor.
Any help would be appreciated.
Thanks
Kevin
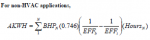
Reminder:
N = The total number of defined combinations of load and Hours. (e.g., 1=10% of the hours at 100% load; 2=20% of
the hours at 83% load, etc.)
BHPN = the HP required by the load at combination N
hoursN=the time, in hours, that is spent at combination N
I have this formula, BHP = E x √3 x I x Percent Efficiency x PF/746, but the utility reminder is confusing me, and when I research the BHP it is refered to the demand of the compressor.
Any help would be appreciated.
Thanks
Kevin