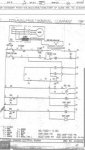
Just get on the phone and call Allen Bradley Technical support. I am reasonably sure you can do this with a PLC, but there are probably devices that will do it mechanically also.View attachment 7907This is a hydraulically operated compactor. The machine is hooked to a 40 yard compactor. When I push start now it runs forward then back and shuts off. I want to be able to push the start button and have it cycle three times. I have tried timers but the speed of the ram is always different depending on the material it is compacting. I have attached a copy of the schematic any help is greatly appreciated. If you can help can you also show me how to alter the schematic to make it work.
Agree. PLC wouldn't need to be anything more than a so-called micro-controller. Perhaps all that is needed is a counting relay.... I am reasonably sure you can do this with a PLC, but there are probably devices that will do it mechanically also.
Ooops...!!! Just realized that comment should have been directed to Ryan.....
[Strathead, your schematic is too small to discern pertinent details.]
Generally speaking, smart relay is just another term for a micro-controller or micro-PLCI'd probably use a smart relay, most manufacturers have one. Or a Click PLC from Automation Direct. Both are super easy to program.
Agree. PLC wouldn't need to be anything more than a so-called micro-controller. Perhaps all that is needed is a counting relay.
[Strathead, your schematic is too small to discern pertinent details.]
I can't get the pic to load bigger but here is a link to another forum I posted on. Hope I'm not breaking any posting rules. http://www.electriciantalk.com/f28/making-industrial-compactor-repeat-48523/#post900464
The "counting relay" is likely the easiest thing to incorporate into whatever controls are already there, they are not that easy to read.
Been a while since I've dealt with count control, but what I gather from looking at a few such products is that most use a DC-triggered count input. That would require additional interfacing for an AC control circuit.Check with Eaton. They have count control which used to be sold (it may still be) under the "Durant" name.
What you are asking to do should be easily done with this product at a reasonable price.
Been a while since I've dealt with count control, but what I gather from looking at a few such products is that most use a DC-triggered count input. That would require additional interfacing for an AC control circuit.
Does anyone know of a simple counting relay that uses an on-off AC 60Hz input?
Short of that, I'm now leaning more towards a "smart relay" as the better option. A "smart relay" could replace T1, and depending on its I/O configuration, possibly R1, R2, and/or R3.
That is a likely possibility that I considered... includes what I meant about interfacing and also why I asked for more detailed info on existing relays. I sometimes forget to be simple and blunt about what I am thinking... I don't recall that a DC trigger is required. It may be that a simple dry type contact closure would be required....
I would have to get familiar with the schematic in order to find where I can get a cycle complete ontact closure to initiate the count countrol to close the contact in the start circuit to recycle the compactor at the end of the first cycle repeating the cycle two more times before allowing it to stop.