mayanees
Senior Member
- Location
- Westminster, MD
- Occupation
- Electrical Engineer and Master Electrician
I'm looking at a system that has six 450 hP, 480V Cooling Water Pump motors powered from three networked 1500 kVA transformers. The transformers power three switchboards, that power the six motors. The soft-starts for the six motors are located approximately 60 feet from the switchboards. The motor disconnect switches are located 120-180 feet from the soft-starts, and the motors are located ten feet from each disconnect.
The problem they're experiencing is the wiring and blades in the disconnect switches are melting.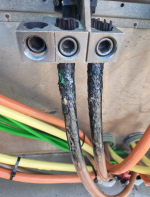
The Eaton soft-starts, model S811+V65N3S, have internal bypass contactors that engage when the motor is up to speed.
I have determined that the switches are underrated for the application because they're unfused and it's written clearly on them that they're only good for 10kA if not outfitted with or protected by Class L fuses, and they're not. But that's a fault current thing so I don't believe it's causing this problem.
Otherwise the circuit meets NEC criteria for motors as the cable is sized appropriately. The motor is rated at 531 amps fla, and the cable is two parallel 400 kCMILs for an ampacity of 670 amps.
Eaton's manual says you can have up to 100 meters between the soft-start and the motor before needing any kind of a load reactor. They have experienced this problem on a number of the six applications, including some motor failures. It's been in service since 2014, and started experiencing problems when demand dropped for the chilled water during Covid a couple years ago. Now they're getting ready for full service this coming May/June.
Any thoughts as to why this application is experiencing failures in the disconnect switches? I don't think it has anything to do with the switches only being rated for 10kA, even though the available fault current is around 35kA, since this would only show during a fault. I understand the load to have around a 2000-amp inrush at startup reaching run speed pretty quickly in a couple seconds.
Thanks for any suggestions.
The problem they're experiencing is the wiring and blades in the disconnect switches are melting.
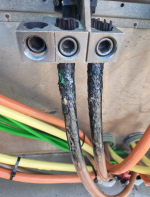
The Eaton soft-starts, model S811+V65N3S, have internal bypass contactors that engage when the motor is up to speed.
I have determined that the switches are underrated for the application because they're unfused and it's written clearly on them that they're only good for 10kA if not outfitted with or protected by Class L fuses, and they're not. But that's a fault current thing so I don't believe it's causing this problem.
Otherwise the circuit meets NEC criteria for motors as the cable is sized appropriately. The motor is rated at 531 amps fla, and the cable is two parallel 400 kCMILs for an ampacity of 670 amps.
Eaton's manual says you can have up to 100 meters between the soft-start and the motor before needing any kind of a load reactor. They have experienced this problem on a number of the six applications, including some motor failures. It's been in service since 2014, and started experiencing problems when demand dropped for the chilled water during Covid a couple years ago. Now they're getting ready for full service this coming May/June.
Any thoughts as to why this application is experiencing failures in the disconnect switches? I don't think it has anything to do with the switches only being rated for 10kA, even though the available fault current is around 35kA, since this would only show during a fault. I understand the load to have around a 2000-amp inrush at startup reaching run speed pretty quickly in a couple seconds.
Thanks for any suggestions.