confused-engineer81
Member
- Location
- Denver
- Occupation
- Electrical Engineer
Is using the 60Hz cables in SKM's equipment library close enough to their 50Hz counterparts. If not, how do I find information for Copper, Aluminum, in both magnetic and non magnetic conduit in all typical trade sizes so I can accurately model a 50Hz System in SKM?
I'm working on a project that uses a 50Hz electrical system. In SKM there is an option to run studies in 50Hz instead of 60Hz, which I have set correctly. My confusion is that there are cables listed as 50Hz, and cables listed as 60Hz in the SKM library (see image below). I've spot checked similar trade size, quantity, material, etc. the cables have different reactance and resistance values. I understand that Reactance is a function of Hz, so the same cable with 60Hz vs 50Hz would give different Impedances. The options for 50Hz cables in the SKM library are extremely limited and I need more cable types (magnetic vs non magnetic conduit, etc.)
I've tried googling the problem and searching this forum for other answers, but couldn't find anything. SKM tech support doesn't have these on file and asked me to provide them with the cable information. Which i don't know where to find.
If not an answer, I would even appreciate some guidance on where to look to find the information
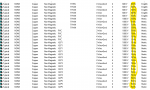
I'm working on a project that uses a 50Hz electrical system. In SKM there is an option to run studies in 50Hz instead of 60Hz, which I have set correctly. My confusion is that there are cables listed as 50Hz, and cables listed as 60Hz in the SKM library (see image below). I've spot checked similar trade size, quantity, material, etc. the cables have different reactance and resistance values. I understand that Reactance is a function of Hz, so the same cable with 60Hz vs 50Hz would give different Impedances. The options for 50Hz cables in the SKM library are extremely limited and I need more cable types (magnetic vs non magnetic conduit, etc.)
I've tried googling the problem and searching this forum for other answers, but couldn't find anything. SKM tech support doesn't have these on file and asked me to provide them with the cable information. Which i don't know where to find.
If not an answer, I would even appreciate some guidance on where to look to find the information
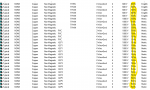