A different idea that may or may not work for your layout.
I had a customer in an very old plant with a hodgepodge of compressors, aftercoolers, refrigerated dryers, oil and water separator tank.
It had air line trunk 3" piping that fed four buildings and a couple of storage tanks. The trunk and distribution piping installation was horrendously installed and modified over the years and more resembled, plumbing drain P traps than a trunk line arranged to drain.
In one of the buildings we had installed a production line for making refractory cement. The equipment kept malfunctioning due to water, oil and rust clogging the valves on the dust collectors cleaning solenoids and the robot packaging line. The air lines and equipment had at least a dozen of the small automatic drain valves you show, scattered about. Problem was it still didn't drain the lines, some due to the piping holding water in trap sections, and the drain valves were clogging due to oil and rust particles. Those automatic drains usually have 1/4" NPT fittings and the internal port openings are 1/8". Way too small to pass the rust chunks and oil sludge that the old pipes contained.
The solution that I used was to make a drain manifold with one timer and one solenoid that had ports large enough to pass the rust chunks and sludge from the old equipment. Collect all of the water, chunks and sludge to one location using 3/8" ID tubing. Then run the the output from the manifold to the oil and water separator, to properly dispose of the oil and drain off the water. Some of the equipment had it own internal automatic drain solenoids and some that just had static drain ports. So the automatic drain manifold was built to accommodate both types.
Partial example at the start.
Completed installation.
Manifold Detail.
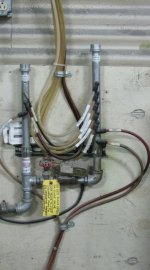
10 Automatic drains replaced (chords eliminated) all waste collected back to a central disposal location.
It's been working fine for the last 13 years.