4x4dually
Senior Member
- Location
- Stillwater, OK
- Occupation
- Electrical Engineer/ Ex-Electrician
We have a test setup in our lab that simulates shipboard, corner grounded delta power. We are required to power some of the distribution racks this way because the Eaton power distribution units require the main and secondary inputs to be 120 degrees apart. If we try to simply power each input with different phases of the facility power, the units will ding with errors.
We are now planning on moving our lab equipment across the street. That brought me back to looking at this circuit again and now I'm questioning something. I've done a little research online and haven't exactly found the question I have answered specifically.
The question I have is do we tie the ECGs and the GEC together like we have it now in the first diagram below? This is how it's been for a while now and I am kind of scared of it honestly. Or do we corner ground the delta with the GEC which is eventually bonded to the EGCs at the first means of disconnect in the facility as shown in the second diagram below? It seems unnatural to me to tie the neutrals and the grounds together at basically the unit under test plug. Naturally I'm inclined to keep them separate but I'm also hesitant to change something we've tested product with and delivered to the customer as "passed."
Any advice on the CGD setup would be great. Thanks in advance.
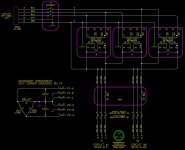
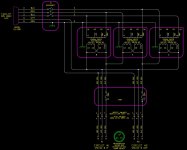
We are now planning on moving our lab equipment across the street. That brought me back to looking at this circuit again and now I'm questioning something. I've done a little research online and haven't exactly found the question I have answered specifically.
The question I have is do we tie the ECGs and the GEC together like we have it now in the first diagram below? This is how it's been for a while now and I am kind of scared of it honestly. Or do we corner ground the delta with the GEC which is eventually bonded to the EGCs at the first means of disconnect in the facility as shown in the second diagram below? It seems unnatural to me to tie the neutrals and the grounds together at basically the unit under test plug. Naturally I'm inclined to keep them separate but I'm also hesitant to change something we've tested product with and delivered to the customer as "passed."
Any advice on the CGD setup would be great. Thanks in advance.
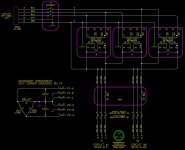
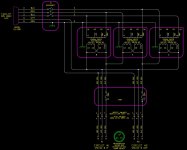