4x4dually
Senior Member
- Location
- Stillwater, OK
- Occupation
- Electrical Engineer/ Ex-Electrician
Getting into something that I've not done before and thought I'd ask if anyone has delt with this type of design. Any constructive feedback would be greatly appreciated.
I'm designing a test panel that will allow DMM probing on the 115 VAC circuits. This probing will allow personnel the ability to fault isolate bad components without the need to remove equipment. The circuits will be 115 VAC line to return; however, when installed on the ships, it will actually be 58 L-G, 58 Return-G. Since there isn't a bonded "neutral", I think I need to current limit the line and return points equally.
I would like to provide user safety by conducting voltage readings or absence of voltage testing without the risk of accidental contact with live electrical components. I'm assuming this could be accomplished with something as simple as an in-line resistor but I'm just now starting to research how it is done. I always over simply things so I thought I'd ask if anyone has a good working knowledge of this setup.
I've been digesting this page but as with most pages, they talk a lot of jargon and never give an approved circuit or method for actually doing it. Typical of most regulatory bodies....they like to make rules but they can't tell you how to meet them.
ohsonline.com
Any feedback would be great!!!
I'm designing a test panel that will allow DMM probing on the 115 VAC circuits. This probing will allow personnel the ability to fault isolate bad components without the need to remove equipment. The circuits will be 115 VAC line to return; however, when installed on the ships, it will actually be 58 L-G, 58 Return-G. Since there isn't a bonded "neutral", I think I need to current limit the line and return points equally.
I would like to provide user safety by conducting voltage readings or absence of voltage testing without the risk of accidental contact with live electrical components. I'm assuming this could be accomplished with something as simple as an in-line resistor but I'm just now starting to research how it is done. I always over simply things so I thought I'd ask if anyone has a good working knowledge of this setup.
I've been digesting this page but as with most pages, they talk a lot of jargon and never give an approved circuit or method for actually doing it. Typical of most regulatory bodies....they like to make rules but they can't tell you how to meet them.
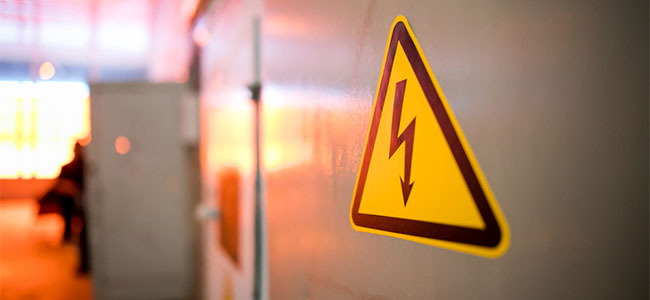
Understanding ‘Point of Work’ in NFPA 70E -- Occupational Health & Safety
How permanent absence of voltage test points ensure compliance and safety.
Any feedback would be great!!!