310 BLAZE IT
Senior Member
- Location
- NJ
Hello,
I am sizing a PV source circuit and I am trying to remember how code handles the DC input circuits (and why):
I have an inverter with a maximum input current of 180A. If the current exceeds this amount, my understanding was that the MPPT will adjust to a higher voltage by increasing its impedance and derate the input power while keeping the input current below this value. Using 690.8(A)(1)(a)(2) does not explicitly state that the inverter limiting the input current is the reason for allowing an exception to this rule, however I believe it should be.

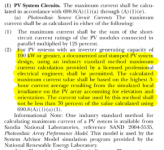
If I go into SAM which is reccomended in the note below, I get a maximum hourly current of ~11.5Ax 15 strings = ~172A
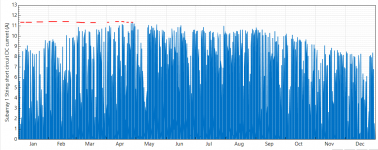
Now if I crank up the DC:AC ratio, the same current appears despite the clipping losses being quite high, meaning SAM is incorrect:
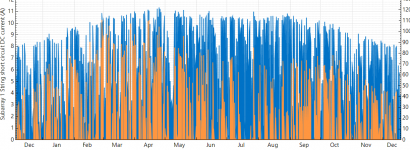
the PE seal should not be needed for overloading the conductors but rather overloading the inverter in accordance with mfr requirements, so I feel this code section should be revised to reflect this and not reference SAM...
Thoughts?
I am sizing a PV source circuit and I am trying to remember how code handles the DC input circuits (and why):
I have an inverter with a maximum input current of 180A. If the current exceeds this amount, my understanding was that the MPPT will adjust to a higher voltage by increasing its impedance and derate the input power while keeping the input current below this value. Using 690.8(A)(1)(a)(2) does not explicitly state that the inverter limiting the input current is the reason for allowing an exception to this rule, however I believe it should be.

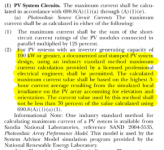
If I go into SAM which is reccomended in the note below, I get a maximum hourly current of ~11.5Ax 15 strings = ~172A
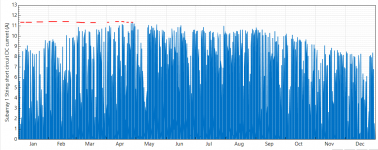
Now if I crank up the DC:AC ratio, the same current appears despite the clipping losses being quite high, meaning SAM is incorrect:
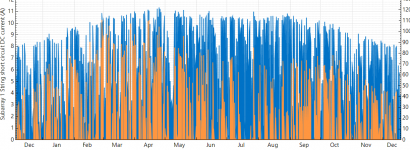
the PE seal should not be needed for overloading the conductors but rather overloading the inverter in accordance with mfr requirements, so I feel this code section should be revised to reflect this and not reference SAM...
Thoughts?