Willie Snyder
Co-Host High Voltage Live Podcast
- Location
- Denver, Co
- Occupation
- Electrical Foreman / Certified NICET II Fire alarm technician
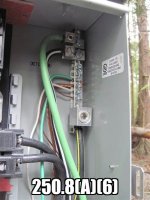
Non-conductive coatings are not required to be removed to bond electrical equipment because modern bonding methods and materials can effectively penetrate these coatings to establish a reliable electrical connection. These coatings, often applied for protection against corrosion or environmental damage, do not significantly impede the bonding process due to the following reasons:
- Penetrative Bonding Techniques: Many bonding methods, such as the use of self-piercing fasteners or specialized conductive adhesives, can penetrate non-conductive coatings, ensuring a good electrical contact without the need to remove the coating.
- Enhanced Conductive Materials: Some bonding systems incorporate materials with enhanced conductive properties that can establish an electrical connection through thin non-conductive layers.
- Regulatory Acceptance: Electrical codes and standards have evolved to recognize the effectiveness of modern bonding techniques that do not require the removal of non-conductive coatings, provided they meet specific performance criteria.