There are many opinions regarding grounding and earth equipotential rods in PV systems installations. I hope you could help me with this topic guys.
The installer and inverter company gave me some ideas about earthing pv systems and I have set SPD protections right before entering into the building. I though that 3 independent rods in triangle right near the solar array to connect PV and SPDs would be a better idea that running any EGC throughout the building or bonding GEC to the building rods. Im a bit worried about voltage induction between isolated earth rods and also about closed loops if we equipotential them.
WHAT DO YOU THINK ABOUT THE CONFIGURATION? I NEED YOUR HELP.
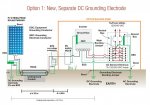
The SPDs will be installed outside with IP65 box, they will be connected by EGC to the PV electrodes bar (as you guys can see on the pic). To ground that box, can I use the same EGC or should I run another wire for it?
Looking forward to hearing from you,
thank in advance
The installer and inverter company gave me some ideas about earthing pv systems and I have set SPD protections right before entering into the building. I though that 3 independent rods in triangle right near the solar array to connect PV and SPDs would be a better idea that running any EGC throughout the building or bonding GEC to the building rods. Im a bit worried about voltage induction between isolated earth rods and also about closed loops if we equipotential them.
WHAT DO YOU THINK ABOUT THE CONFIGURATION? I NEED YOUR HELP.
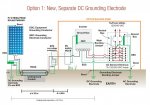
The SPDs will be installed outside with IP65 box, they will be connected by EGC to the PV electrodes bar (as you guys can see on the pic). To ground that box, can I use the same EGC or should I run another wire for it?
Looking forward to hearing from you,
thank in advance