Andres Arias
PV Solar engineer
- Location
- New York
- Occupation
- Electrical Engineer
Good evening.
I have an inquire in regards on how to choose the OCPD for a motor, given that sometimes I see that it is chosen to the next higher standard and sometimes to the next lower standard OCPD in Art 240. See below the following question (3.1K):
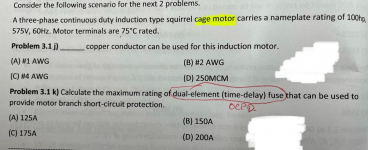
As per Table 430.250 for this motor the FLC is 99A. Then in Table 430.52, the factor to apply to this FLC is 1.75, which turns out in 173.25A. Then we go to Art 240 to choose the OCPD, which as far I understand for motors, should be chosen to the next lower standard OCPD (as opposed when choosing an OCPD for wires which is the next higher, contingent upon the current is less or larger than 800 A), that is 150A. However in the solution provided by the textbook (Study guide for PE exam), the OCPD chosen is 175A. See below the solution of the book:
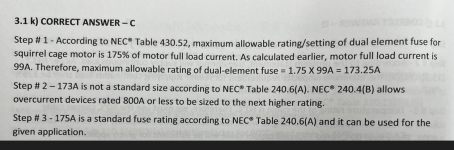
When dealing with motors, how to choose the OCPD in Art 240?
Thank you beforehand for your collaboration.
I have an inquire in regards on how to choose the OCPD for a motor, given that sometimes I see that it is chosen to the next higher standard and sometimes to the next lower standard OCPD in Art 240. See below the following question (3.1K):
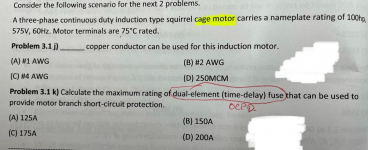
As per Table 430.250 for this motor the FLC is 99A. Then in Table 430.52, the factor to apply to this FLC is 1.75, which turns out in 173.25A. Then we go to Art 240 to choose the OCPD, which as far I understand for motors, should be chosen to the next lower standard OCPD (as opposed when choosing an OCPD for wires which is the next higher, contingent upon the current is less or larger than 800 A), that is 150A. However in the solution provided by the textbook (Study guide for PE exam), the OCPD chosen is 175A. See below the solution of the book:
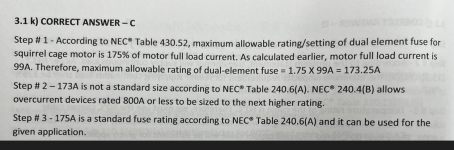
When dealing with motors, how to choose the OCPD in Art 240?
Thank you beforehand for your collaboration.