I'm interested in measuring demand (average) voltage, current, apparent power, and power factor on the load side of an SCR power controller (Watlow DT-348) feeding a delta-connected 480VAC three-phase heater. I need all three legs measured independently, which is why I can't use the SCR power controller's own diagnostics. I'm looking at an AB Power Monitor 500. I understand that power monitors can have issues with drive outputs due to voltage spikes and/or harmonics, so we would use a zero-crossing or burst-firing method of control which as I understand it minimizes those concerns. Does anyone see a reason why this wouldn't work? If the demand calculation is averaging over the duty cycle of the firing period, I believe I should get what I want. I did talk to Rockwell about this, and they say it is not recommended, but I'm not sure they fully understood the application. I will continue engaging with them, but wanted to get a second opinion.
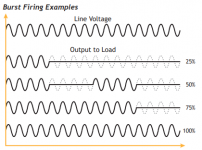
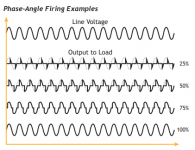
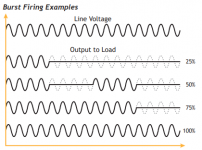
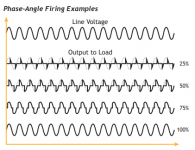