- Location
- San Francisco Bay Area, CA, USA
- Occupation
- Electrical Engineer
Just a cautionary tale.
I have a situation right now where we put in some VFDs on pumps, even AFTER double checking the motor nameplate FLAs, and are now being told that the pump OEM was intending on running the motors into the Service Factor continuously, so they are saying we sized the VFDs incorrectly (we were not told that).
Just so everyone knows, when you run a motor with a 1.15 Service Factor from a VFD, the motor NO LONGER HAS A SERVICE FACTOR! Most "inverter duty" motors state that right on the motor nameplate (they did in this case) by showing that if run from an inverter, the Service Factor is 1.0. Non inverter duty motors might not state that on the nameplate since the motor mfr will tell you they are not meant to be run on an inverter drive, but if you ask, they will tell you, no service factor.
Here's an example (not from this project, but another one I am working on right now where we had a similar issue in that the Engineer insisted on sizing the VFD to the Service Factor Amps).
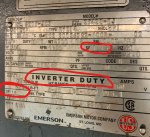
The issue is that "Service Factor" is a mainly thermal issue in that the motor is designed to handle 115% more heat than a full rated load would create in the motor, so if you overload it, it will be able to handle that. Years ago NEMA specs used to say "temporarily", but they took that out at some point and all it says now is some weasel words to the effect of "running a motor into the Service factor may result in decreased motor performance and life". But running a motor on a VFD (inverter drive) creates additional heating in the motor too, so the 1.15SF motor can handle EITHER an overload of 115%, OR running on an inverter, but not both. Apparently some OEMs and MEs are unaware of this fact and it can bite you if you are the one supplying the VFD.
I have a situation right now where we put in some VFDs on pumps, even AFTER double checking the motor nameplate FLAs, and are now being told that the pump OEM was intending on running the motors into the Service Factor continuously, so they are saying we sized the VFDs incorrectly (we were not told that).
Just so everyone knows, when you run a motor with a 1.15 Service Factor from a VFD, the motor NO LONGER HAS A SERVICE FACTOR! Most "inverter duty" motors state that right on the motor nameplate (they did in this case) by showing that if run from an inverter, the Service Factor is 1.0. Non inverter duty motors might not state that on the nameplate since the motor mfr will tell you they are not meant to be run on an inverter drive, but if you ask, they will tell you, no service factor.
Here's an example (not from this project, but another one I am working on right now where we had a similar issue in that the Engineer insisted on sizing the VFD to the Service Factor Amps).
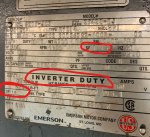
The issue is that "Service Factor" is a mainly thermal issue in that the motor is designed to handle 115% more heat than a full rated load would create in the motor, so if you overload it, it will be able to handle that. Years ago NEMA specs used to say "temporarily", but they took that out at some point and all it says now is some weasel words to the effect of "running a motor into the Service factor may result in decreased motor performance and life". But running a motor on a VFD (inverter drive) creates additional heating in the motor too, so the 1.15SF motor can handle EITHER an overload of 115%, OR running on an inverter, but not both. Apparently some OEMs and MEs are unaware of this fact and it can bite you if you are the one supplying the VFD.