Dolomite
New member
- Location
- Holland, MI
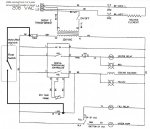
Hello everyone – first post – short-time lurker,
I work in an electrical testing lab which mostly focuses on testing automotive batteries. A typical test set-up would involve setting a dozen lead-acid batteries into a temperature controlled water tank (steel) and then connecting the battery leads to a multi-channel battery cycler which will take the batteries through a programmed series of charges and discharges.
Keeping the water line at an appropriate level has always been somewhat of a challenge; the original system that was in place for this task involved a (appliance) dryer timer which would activate the water inlet valve (called the “Cooling Solenoid” in the drawing) for a few minutes every half-hour. Any excess water would flow into an elevated drain (an 8” length of PVC threaded into the tank’s drain). The problem with the timers was that, in addition to wasting water, they would stop working after a few months.
Enter the quick fix: At some point somebody got rid of the timer and wired in a magnetic float switch (as shown in the drawing) – and I must say it’s been working fairly well. However, I am not crazy about 120VAC being passed through the submerged float switch since mine and my co-worker’s hands are in frequent contact with the tank water.
One of my co-workers is insistent that the GFCI located in the panel will protect us – but I pointed out that the 208/115 transformer effectively isolates the 208V GFCI in the panel from the 120VAC that is running the controller, pump and relays – and should the float switch enclosure ever crack allowing tank water to contact the 120VAC, we will be at the mercy of that 4 Amp fuse – which would not be funky at all.
I could use a little help with identifying or citing any relevant NEC codes we may be straying away from. I could also use some advice as to how to remedy this situation, namely if I were to remove the 120VAC going to the float switch and substitute it with a relay with a 5VDC coil to switch the 120VAC going to the “cooling solenoid”. If the float switch were to fail, I would think that 5V in the water would not cause a serious shock – am I right or wrong about that?
Thanks for reading all of this.