dave154304
Member
- Location
- Wisconsin
Hello,
I've been asked a question about a reversible single phase motor setup that I can't answer. I've attached a picture to help describe what I'm working with. In this system, we turn 120V onto wire 22231 for the motor to go one way, and 120V on wire 22241 for it to go the other way. Wire 10091 is a 120V common. The design has been in place for many years and historically, the duty cycle on this motor was very low - the motor might make an adjustment every day or two. If it reversed, it was human controlled, so there were seconds between CW and CCW commands. There were never any complaints about the operation of this system.
Now, a new requirement has been added and new software developed where we are making this motor more active. With this change, the motor can be making moves 2-3X (in different directions) in 10 seconds (i.e. go CW for 2 seconds, CCW for 6 seconds, and CW for 2 seconds). It is possible that the moves are close to each other, for instance one move could stop and 50 msec later the reverse move start. The two signals are never on at the same time. The question that was posed to me is that sometimes the software tells the motor to go CCW, but the motor actually turns CW. This doesn't happen often, but regularly enough that bugs in the software have been eliminated.
Can anybody explain the details of how the CAP and RES change this circuit to make the reverse happen? I'm not an expert in this system...it has been in place for 25+ years and just gets carried forward.
If the motor hasn't stopped moving in one direction before the reverse signal fires, could reversing it so quickly possible make it not reverse?
Would strange things potentially happen if the motor was being back driven a little when the signal to turn in a direction happened? I'm thinking as the motor is working like a generator that something strange is happening with the command voltage?
Are there any other theories about anything that could cause this?
Thanks in advance everybody.
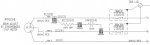
I've been asked a question about a reversible single phase motor setup that I can't answer. I've attached a picture to help describe what I'm working with. In this system, we turn 120V onto wire 22231 for the motor to go one way, and 120V on wire 22241 for it to go the other way. Wire 10091 is a 120V common. The design has been in place for many years and historically, the duty cycle on this motor was very low - the motor might make an adjustment every day or two. If it reversed, it was human controlled, so there were seconds between CW and CCW commands. There were never any complaints about the operation of this system.
Now, a new requirement has been added and new software developed where we are making this motor more active. With this change, the motor can be making moves 2-3X (in different directions) in 10 seconds (i.e. go CW for 2 seconds, CCW for 6 seconds, and CW for 2 seconds). It is possible that the moves are close to each other, for instance one move could stop and 50 msec later the reverse move start. The two signals are never on at the same time. The question that was posed to me is that sometimes the software tells the motor to go CCW, but the motor actually turns CW. This doesn't happen often, but regularly enough that bugs in the software have been eliminated.
Can anybody explain the details of how the CAP and RES change this circuit to make the reverse happen? I'm not an expert in this system...it has been in place for 25+ years and just gets carried forward.
If the motor hasn't stopped moving in one direction before the reverse signal fires, could reversing it so quickly possible make it not reverse?
Would strange things potentially happen if the motor was being back driven a little when the signal to turn in a direction happened? I'm thinking as the motor is working like a generator that something strange is happening with the command voltage?
Are there any other theories about anything that could cause this?
Thanks in advance everybody.
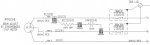