CelectricB
Member
- Location
- Texas Panhandle
- Occupation
- MEP Designer
Hi all,
I have a relatively simple question concerning wire size. Consider the screenshot below.
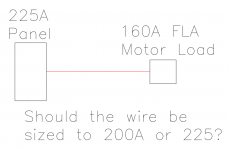
I understand that, per code, the wire may be sized to 125% FLA making it 200A. My question is, suppose the motor load malfunctioned or inrush current sustained too long, and it draws 210A, is this not an issue that we consider? It makes more sense to me that the wire be sized to OCP so as not to allow more amperage through the wire than it can supply. Thanks in advance!
I have a relatively simple question concerning wire size. Consider the screenshot below.
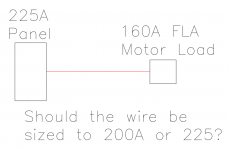
I understand that, per code, the wire may be sized to 125% FLA making it 200A. My question is, suppose the motor load malfunctioned or inrush current sustained too long, and it draws 210A, is this not an issue that we consider? It makes more sense to me that the wire be sized to OCP so as not to allow more amperage through the wire than it can supply. Thanks in advance!