olly
Senior Member
- Location
- Berthoud, Colorado
- Occupation
- Master Electrician
Hey guys,
I have a situation where a very expensive pump that is only lasting about 1 year before failing. The pump is pulling a load of 9A when working properly so I am told by the manufacture. It is on a dedicated 20A circuit. 12 AWG wire the entire length of the 150' circuit except a 18 AWG extension cord that was found 50' from the source. I removed the 18 AWG and installed a 12 AWG wire in its place. This is a 120v pump. It does run 24/7. Its an aeration pump for a lake. It blows air to oxygenize the lake for lake health
I am wondering if this fix / removing the 18 AWG week link will fix the issue?
The pump says voltage of 110v.
The damaged pump / not working pump was pulling 4 amps and I tested voltage while running and got 119v. 122V at the panel. The pump has no thermal overload just a capacitor and the pump.
Do you think removing the 18 AWG wire will fix the problem of the pump failing after a year?
Do you have any recommendations to where to go from here?
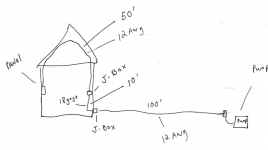
I have a situation where a very expensive pump that is only lasting about 1 year before failing. The pump is pulling a load of 9A when working properly so I am told by the manufacture. It is on a dedicated 20A circuit. 12 AWG wire the entire length of the 150' circuit except a 18 AWG extension cord that was found 50' from the source. I removed the 18 AWG and installed a 12 AWG wire in its place. This is a 120v pump. It does run 24/7. Its an aeration pump for a lake. It blows air to oxygenize the lake for lake health
I am wondering if this fix / removing the 18 AWG week link will fix the issue?
The pump says voltage of 110v.
The damaged pump / not working pump was pulling 4 amps and I tested voltage while running and got 119v. 122V at the panel. The pump has no thermal overload just a capacitor and the pump.
Do you think removing the 18 AWG wire will fix the problem of the pump failing after a year?
Do you have any recommendations to where to go from here?
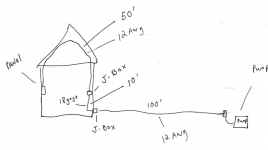