MechEdetour
Member
- Location
- NY, USA
- Occupation
- Design Engineer
Would be nice to get into a discussion about bend space requirements for conductors that are brought into enclosures. The NEC has requirements laid out for installations, and obviously relevant standards also have requirements that manufacturers need to comply with when manufacturing equipment (those requirements are typically duplicated tables pulled from the NEC).
I’ve had some pretty interesting conversations with people and how they interpret the requirements. Some of the verbiage seems to direct people to one table or another when stating what the requirements are. We can argue all day about what is better (especially when we get to conductors in the MCM range) when a large conductor is subject to a 90 deg bend within an 8” gutter to exit an enclosure.
But one thing I am after is how does everyone interpret bend space requirements? I have other questions too, but don’t want to write a first post that fills the whole page . . . already know I’ll have a hard time keeping it short.
Also just to address:
- Not bend radius (as related to integrity of the insulation of a conductor), but space required to bend/route conductors.
- Strictly looking for a requirement, not for something that could potentially be more optimal.
NEC 2014
312.6(B)(1) Conductors Not Entering or Leaving Opposite Wall
Table 312.6(A) shall apply where the conductor does not enter or leave the enclosure through the wall opposite its terminal.
Those with the NEC can reference the table, but I will refer to Table 312.6(A) as the “smaller requirement.”
312.6(B)(2) Conductors Entering or Leaving Opposite Wall
Table 312.6(B) shall apply where the conductor does enter or leave the enclosure through the wall opposite its terminal.
I’ll refer to Table 312.6(B) as the “larger requirement.”
Situation “A” is what I see as a representation of a conductor not entering or exiting the opposite wall. The note under table 312.6(A) also states “Bending space at terminals shall be measured in a straight line from the end of the lug or wire connector (in the direction that the wire leaves the terminal) to the wall, barrier, or obstruction.” I have this measurement addressed by dimension “B1” and graphically represented by the yellow arrow to match the verbiage.
The requirement, as I read the NEC and apply the relevant sections for situation “A”, states that dimension “B1” must be 5” for a 300MCM conductor.
Situation “B” is what I see as a representation of a conductor entering or exiting the opposite wall, whether it be “Run 1” or “Run 2.” Note 1 under table 312.6(B) states “Bending space at terminals shall be measured in a straight line from the end of the lug or wire connector in a direction perpendicular to the enclosure wall. I have this measurement addressed by “B2” and graphically represented by the red arrow to once again match verbiage.
The requirement, for this case, states that dimension “B2” must be 10” for a 300MCM conductor.
I’ve referenced several resources such as various UL standards, the NEC handbook, etc. They all bring me back to what I have shown for what is defined as “opposite wall” and which table to apply when exiting different walls.
I’m curious to know how others go through this exercise. I bring this matter up because on a few occasions now, I’ve had people argue that I have the tables backwards, and the “opposite wall” is actually the top of the enclosure. This baffles me considering that if this was true, then the case where you wouldn’t leave the “opposite wall” (top), would then require the use of the other table for the remaining left, right, and bottom walls of the enclosure.
I’m going to leave this here. I actually hope to get into the “why” it is this way, and maybe a bit more into where exactly the dimensions are to be measured from when different terminals come into play. . . but for now what is everyone else’s take?
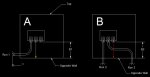
I’ve had some pretty interesting conversations with people and how they interpret the requirements. Some of the verbiage seems to direct people to one table or another when stating what the requirements are. We can argue all day about what is better (especially when we get to conductors in the MCM range) when a large conductor is subject to a 90 deg bend within an 8” gutter to exit an enclosure.
But one thing I am after is how does everyone interpret bend space requirements? I have other questions too, but don’t want to write a first post that fills the whole page . . . already know I’ll have a hard time keeping it short.
Also just to address:
- Not bend radius (as related to integrity of the insulation of a conductor), but space required to bend/route conductors.
- Strictly looking for a requirement, not for something that could potentially be more optimal.
NEC 2014
312.6(B)(1) Conductors Not Entering or Leaving Opposite Wall
Table 312.6(A) shall apply where the conductor does not enter or leave the enclosure through the wall opposite its terminal.
Those with the NEC can reference the table, but I will refer to Table 312.6(A) as the “smaller requirement.”
312.6(B)(2) Conductors Entering or Leaving Opposite Wall
Table 312.6(B) shall apply where the conductor does enter or leave the enclosure through the wall opposite its terminal.
I’ll refer to Table 312.6(B) as the “larger requirement.”
Situation “A” is what I see as a representation of a conductor not entering or exiting the opposite wall. The note under table 312.6(A) also states “Bending space at terminals shall be measured in a straight line from the end of the lug or wire connector (in the direction that the wire leaves the terminal) to the wall, barrier, or obstruction.” I have this measurement addressed by dimension “B1” and graphically represented by the yellow arrow to match the verbiage.
The requirement, as I read the NEC and apply the relevant sections for situation “A”, states that dimension “B1” must be 5” for a 300MCM conductor.
Situation “B” is what I see as a representation of a conductor entering or exiting the opposite wall, whether it be “Run 1” or “Run 2.” Note 1 under table 312.6(B) states “Bending space at terminals shall be measured in a straight line from the end of the lug or wire connector in a direction perpendicular to the enclosure wall. I have this measurement addressed by “B2” and graphically represented by the red arrow to once again match verbiage.
The requirement, for this case, states that dimension “B2” must be 10” for a 300MCM conductor.
I’ve referenced several resources such as various UL standards, the NEC handbook, etc. They all bring me back to what I have shown for what is defined as “opposite wall” and which table to apply when exiting different walls.
I’m curious to know how others go through this exercise. I bring this matter up because on a few occasions now, I’ve had people argue that I have the tables backwards, and the “opposite wall” is actually the top of the enclosure. This baffles me considering that if this was true, then the case where you wouldn’t leave the “opposite wall” (top), would then require the use of the other table for the remaining left, right, and bottom walls of the enclosure.
I’m going to leave this here. I actually hope to get into the “why” it is this way, and maybe a bit more into where exactly the dimensions are to be measured from when different terminals come into play. . . but for now what is everyone else’s take?
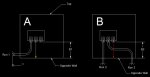