Hello all, I have two questions...
1. I have an elevator motor with the nameplate below... I am trying to figure out what the "starts/hr" has to with the HP rating? Why would that change things? There are not two motors in this location.
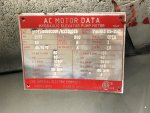
2. This elevator motor is configured with two contacts in a wye-delta (star-delta) configuration. The building is connect on the generator, but when the generator kicks on and the elevator is called, the wye setup starts the motor, but the transition from the open to delta connection won't hold the delta run contactor. The generator has the capacity, but I am thinking the holding contactor is dropping out due to the inrush during at during the delta connection. Anyone have any thoughts, or advice?
Thank you!
1. I have an elevator motor with the nameplate below... I am trying to figure out what the "starts/hr" has to with the HP rating? Why would that change things? There are not two motors in this location.
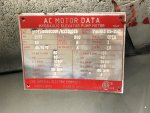
2. This elevator motor is configured with two contacts in a wye-delta (star-delta) configuration. The building is connect on the generator, but when the generator kicks on and the elevator is called, the wye setup starts the motor, but the transition from the open to delta connection won't hold the delta run contactor. The generator has the capacity, but I am thinking the holding contactor is dropping out due to the inrush during at during the delta connection. Anyone have any thoughts, or advice?
Thank you!