What tests? Quite often motor shops will just run a Baker test and treat it as gospel. Far from it! There are a number of faults it will not detect. Putting it on a test stand and running it at least no load and recording the three currents and comparing to typical data is also required.
On your end what condition is the compressor? Does the shaft turn freely or is it locked up? If you can’t turn it by hand there is something wrong and the motor is stalling. Current will read LRA, all three phases.
Also Its a lot of trouble to do this SAFELY and right now with no motor would be the ideal situation but there is nothing wrong with energizing a starter with the motor disconnected at the motor peckerhead to verify everything. Also need to check the primary side of a transformer if one is involved. With a delta-wye transformer if you have a missing primary phase the missing phase will be “regenerated” on the secondary side so measured without a load you will indeed see say close to 480 across the board. But it’s very high impedance and as soon as you apply a load, it suddenly reflects the correct (0) voltage. This will also locate loose connections, ground faults in the feeder cable, etc.
Another common problem with wye delta starters is the timer/current relay fails and it gets stuck in wye mode or one of the aux contacts has failed or the reactor in closed transition types (most are open transition). Also welded contactors can cause this. Open and inspect the contact tips. There are a lot more parts and things to go wrong. That’s why I recommend upgrading to electronic soft starts by the time you need to repair.
it's a hydraulic pump, not a compressor but the guy knows his hydraulics for sure, so I'm assuming he's checked/verified everything is good on the front (i would hope...). he didn't measure the amps when he first attempted to run the motor unfortunately, he will theis time.
i've only been in that building once or twice, i have no idea what kind of setup they have? but this is great info! never considered a missing phase on the primary side of a transformer. and sounds like this could likely be the case bc he did say he checked voltage on all 3 legs but im assuming he did that when the the motor wasn't running? so when he tried to start they motor this voltage could drop like missing phase and giving the humming. he did however go grab another motor (not sure of the size) and run it on the same motor starter set that he has on his test bench and it ran fine, so fairly sure there's no issues there. 100% exact same setup down to the Meltric connector. and he said he's triple checked the continuity and checked for shorts from the Meltric connector to the end of the wires feeding the motor peckerhead
we're not using a Wye/delta starter, i was just confirming that we didn't need one really. other folks were saying we did. its just on a DOL motor starter. There's a soft starter on order for it, it's just not here yet unfortunately. and of course the deadline to test/ship this unit can't move so they're gonna go with what they got for now...
I just got the test report back from them a minute ago, see picture below. their email read:
We had a chance to check out motor.
We checked double checked and inspected the termination connection for 460 volts, WYE.
We also performed electrical testing to motor windings, Surge Comparison Test, And Megger Test.
All passed, We then connected and bench tested for 460 volts, Motor ran good with balanced
no load amps, Bench tested at rated voltage 460 volts, No Load Amps 60, 62, 62.
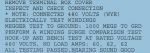