wwhitney
Senior Member
- Location
- Berkeley, CA
- Occupation
- Retired
Contemplating a refresh of a small (12 * 250W panels) PV system installed in 2012. A picture of the end of the bottom corner of one of two rows of panels is below. A couple questions:
1) Does anyone recognize the brand/model of the racking system?
2) The existing modules are 65-1/4" in height and sit between the rails. I assume that panels are not currently produced in that particular height, so no drop in replacement would be available. Is it worthwhile to pursue reusing the rails?
E.g. 67-3/4" seems to be a standard height for 108 cell panels, so that could be accommodated by either mounting the panels to the top of the rails and letting them overhang an inch or so top and bottom, or figuring out how to add an offset piece between the rails and the vertical aluminum posts they are mounted on to increase the spacing by 2-1/2".
Thanks,
Wayne
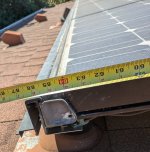
1) Does anyone recognize the brand/model of the racking system?
2) The existing modules are 65-1/4" in height and sit between the rails. I assume that panels are not currently produced in that particular height, so no drop in replacement would be available. Is it worthwhile to pursue reusing the rails?
E.g. 67-3/4" seems to be a standard height for 108 cell panels, so that could be accommodated by either mounting the panels to the top of the rails and letting them overhang an inch or so top and bottom, or figuring out how to add an offset piece between the rails and the vertical aluminum posts they are mounted on to increase the spacing by 2-1/2".
Thanks,
Wayne
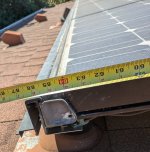