Timpi Electric Solutions
Member
- Location
- Indiana
- Occupation
- Electrician
I'm pulling my hair out over here. I have a customer with a 200HP 480V dust collector. A 400A branch circuit breaker feeds a NEMA contactor, which then feeds a soft starter. All of the other motor loads and controls are supplied from a separate circuit. About two weeks ago, they started having issues with the 400A circuit breaker tripping when attempting to start the main fan.
I used a power energy logger to record the start attempts, and saw that the curve of the soft starter was very abrupt; it very rapidly reached 780 amps, and maintained that current for about 11 seconds until dropping to 125A after reaching running speed. While starting, there would be significant vibration and noise, which is usually present but much more severe.
Suspecting that the current curve was far too steep, I replaced the soft starter with an updated equivalent and replicated the parameters from the original soft starter. Noise and vibration were even more extreme than before replacing the starter, and the soft starter would internally trip every single time but the branch circuit breaker would not. The 400A breaker has not tripped once since replacing the starter.
I made sure not to exceed the starter's rated 4 starts per hour, and worked my way through the circuit from the 400A breaker all the way to the motor terminal box checking terminals and splices for tightness. I checked resistance through the contacts in the the motor disconnect, and it was fine. Still unable to successfully start the motor, I increased the maximum current limit on the starter to 1000A, and the motor was able to start without tripping. I ran it through several startup cycles before calling it quits, as I felt that it would reliably start when 1st shift came in about three hours later.
I replaced the soft starter on 2/7/2024. I stopped by on 2/13/2024 and the maintenance chief let me know that the main fan had tripped one time for the past two mornings. I bypassed the contactor supplying the soft starter and fed the soft starter directly from the 400A breaker, and logged several start cycles, each of which were fine. When I was disconnecting the conductors that connected to the contactor line terminals, I discovered that one of them was slightly loose. I'm not sure if it loosened over the course of the week or if I had missed properly torquing it when I was replacing the soft starter.
I then reconnected the contactor and logged three more start cycles, which showed no difference from the logs with the contactor bypassed. The plant has two 200HP dust collectors, so I then logged three starts with the other dust collector, which also uses a soft starter. The logs were fairly comparable.
All of the tests that I logged on the problem motor had a gentle current curve that reached about 780A before dropping to 125A. I felt that the loose terminal on the contactor had been the cause of the issue, as the current was reasonable and the noise and vibration were normal.
I just got a phone call today that the soft starter tripped internally again this morning on start up. I looked into the data logs more closely and realized that both 200HP motors have pretty significant current imbalances, despite there only being a very small voltage imbalance. I'm at a bit of a loss as how to next proceed.
Here is the startup of the problem motor with contactor bypassed.
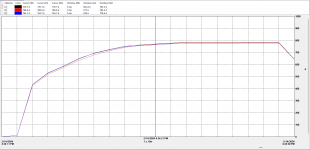
Here's the log of the problem motor with contactor.
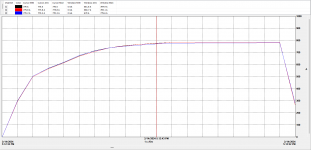
Here's the log of the dust collector that is NOT having issues.
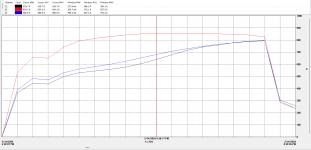
Here's running current of the problem motor with contactor bypassed.
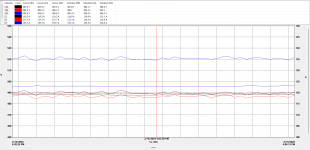
Here's the running current of the problem motor with contactor connected.
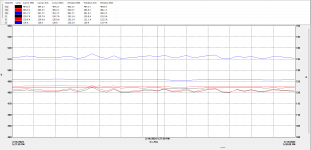
Here's the running current of the motor that is NOT the problem.
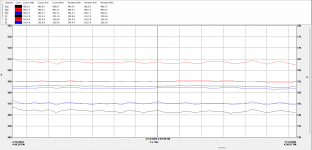
On the graphs of motors at speed, the lines with slight sine waves are current; the flat lines are voltage.
As you can see, both motors are imbalanced, despite the voltage being fairly balanced.
I used a power energy logger to record the start attempts, and saw that the curve of the soft starter was very abrupt; it very rapidly reached 780 amps, and maintained that current for about 11 seconds until dropping to 125A after reaching running speed. While starting, there would be significant vibration and noise, which is usually present but much more severe.
Suspecting that the current curve was far too steep, I replaced the soft starter with an updated equivalent and replicated the parameters from the original soft starter. Noise and vibration were even more extreme than before replacing the starter, and the soft starter would internally trip every single time but the branch circuit breaker would not. The 400A breaker has not tripped once since replacing the starter.
I made sure not to exceed the starter's rated 4 starts per hour, and worked my way through the circuit from the 400A breaker all the way to the motor terminal box checking terminals and splices for tightness. I checked resistance through the contacts in the the motor disconnect, and it was fine. Still unable to successfully start the motor, I increased the maximum current limit on the starter to 1000A, and the motor was able to start without tripping. I ran it through several startup cycles before calling it quits, as I felt that it would reliably start when 1st shift came in about three hours later.
I replaced the soft starter on 2/7/2024. I stopped by on 2/13/2024 and the maintenance chief let me know that the main fan had tripped one time for the past two mornings. I bypassed the contactor supplying the soft starter and fed the soft starter directly from the 400A breaker, and logged several start cycles, each of which were fine. When I was disconnecting the conductors that connected to the contactor line terminals, I discovered that one of them was slightly loose. I'm not sure if it loosened over the course of the week or if I had missed properly torquing it when I was replacing the soft starter.
I then reconnected the contactor and logged three more start cycles, which showed no difference from the logs with the contactor bypassed. The plant has two 200HP dust collectors, so I then logged three starts with the other dust collector, which also uses a soft starter. The logs were fairly comparable.
All of the tests that I logged on the problem motor had a gentle current curve that reached about 780A before dropping to 125A. I felt that the loose terminal on the contactor had been the cause of the issue, as the current was reasonable and the noise and vibration were normal.
I just got a phone call today that the soft starter tripped internally again this morning on start up. I looked into the data logs more closely and realized that both 200HP motors have pretty significant current imbalances, despite there only being a very small voltage imbalance. I'm at a bit of a loss as how to next proceed.
Here is the startup of the problem motor with contactor bypassed.
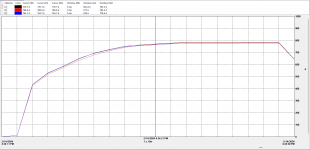
Here's the log of the problem motor with contactor.
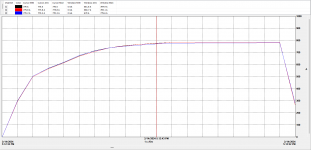
Here's the log of the dust collector that is NOT having issues.
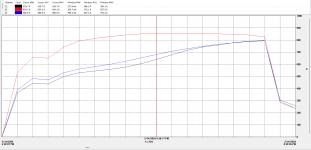
Here's running current of the problem motor with contactor bypassed.
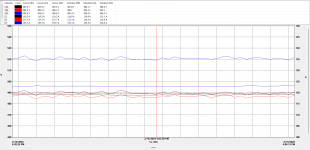
Here's the running current of the problem motor with contactor connected.
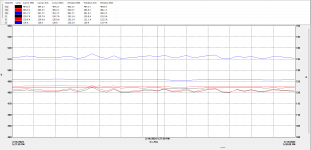
Here's the running current of the motor that is NOT the problem.
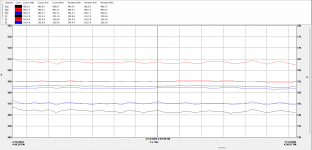
On the graphs of motors at speed, the lines with slight sine waves are current; the flat lines are voltage.
As you can see, both motors are imbalanced, despite the voltage being fairly balanced.