Timpi Electric Solutions
Member
- Location
- Indiana
- Occupation
- Electrician
Voltage unbalance on the service while the dust collector is not running is 1.02%. Technically, it exceeds NEMA standards, but only by 0.02%.
Voltage unbalance with the dust collector IS running is 0.95%.
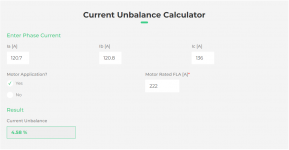
Using the my motor's FLA of 222A, unbalance is only 4.58% while running.
While starting, motor current unbalance is only 0.49%.
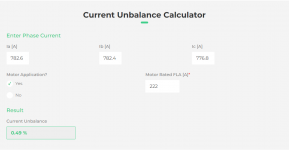
Voltage unbalance with the dust collector IS running is 0.95%.
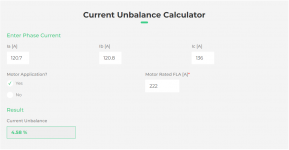
Using the my motor's FLA of 222A, unbalance is only 4.58% while running.
While starting, motor current unbalance is only 0.49%.
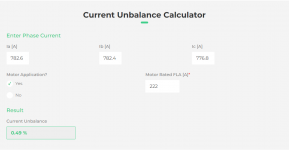