Vankirk Electric SR. PM
Member
- Location
- Winder, Ga
Scenario:
An inspector in San Jose, CA is telling us that we can't use split bolts for our motor lead connections. We have (1) 3/0 per phase feeding the 3-phase motor. The motor has (4) #8 conductors per phase. We need a solution for connecting the 3/0 to the (4) #8's... keep in mind that space is limited since we are working in the small junction space of the pump. Picture below shows you what we currently have with the split bolts. Thanks for the help.
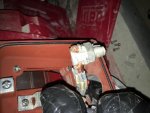
An inspector in San Jose, CA is telling us that we can't use split bolts for our motor lead connections. We have (1) 3/0 per phase feeding the 3-phase motor. The motor has (4) #8 conductors per phase. We need a solution for connecting the 3/0 to the (4) #8's... keep in mind that space is limited since we are working in the small junction space of the pump. Picture below shows you what we currently have with the split bolts. Thanks for the help.
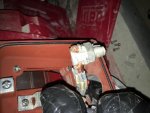