dwinkels
New member
- Location
- Sacramento, CA
Has anyone experienced a similar issue:
Single head, 30' road/lot poles are experiencing unusual fatigue and cracking above the weld, where the base connects to the pole. Two of these poles have completely failed and have fallen over (see attached picture). Approximately nineteen more have been identified with significant cracking above the weld (see attached picture) - these poles were taken down for safety concerns. There are 106 poles total. The poles are on site at a Federal Penitentary located at a remote site in the Central Valley of California. This area is not typically described or known as a high-wind area. AASHTO and ASCE wind maps place this region in the lowest zone on their wind chart. The pole in question is a Cooper, 5" x 30' square, straight, steel pole with an 11" diameter base plate. The wall thickness is .120". It has one 400W Metal Halide Fixture affixed to it. According to White Papers published by Cooper, the damage is attributed to pole vibration - more specifically a phenomena identifed as Vortex Shedding (Second Mode Vibration). This is caused by winds, but is not necessarily attributed to high winds or gusts. On the day these two poles fell, the gusts did not exceed 50 mph, which is well within the allowable range of winds that this pole is designed to handle. This situation has occured at other locations, and for some reason, it is only the combination of the 5" x 30' square, straight, steel pole with a single head affixed to it that experiences the pole fatique. Similar pole/ fixture configurations that are taller and similar poles of the same height and design but with two or three heads seem to not be affected. Unfortunatley, Cooper excludes this from their warranty. Why they would allow this combination to be sold is uncertain to me and is a topic for a different forum. My question to readers that can identify with this problem is how did you ultimately resolve this? To what level did Cooper get involved. What pole did you replace with? Did you replace similar poles that showed no signs of cracking? How did you handle the warranty with the owner, general contractor, distributor and manufacturer? Is there anything I seem to be overlooking or not considering?
Single head, 30' road/lot poles are experiencing unusual fatigue and cracking above the weld, where the base connects to the pole. Two of these poles have completely failed and have fallen over (see attached picture). Approximately nineteen more have been identified with significant cracking above the weld (see attached picture) - these poles were taken down for safety concerns. There are 106 poles total. The poles are on site at a Federal Penitentary located at a remote site in the Central Valley of California. This area is not typically described or known as a high-wind area. AASHTO and ASCE wind maps place this region in the lowest zone on their wind chart. The pole in question is a Cooper, 5" x 30' square, straight, steel pole with an 11" diameter base plate. The wall thickness is .120". It has one 400W Metal Halide Fixture affixed to it. According to White Papers published by Cooper, the damage is attributed to pole vibration - more specifically a phenomena identifed as Vortex Shedding (Second Mode Vibration). This is caused by winds, but is not necessarily attributed to high winds or gusts. On the day these two poles fell, the gusts did not exceed 50 mph, which is well within the allowable range of winds that this pole is designed to handle. This situation has occured at other locations, and for some reason, it is only the combination of the 5" x 30' square, straight, steel pole with a single head affixed to it that experiences the pole fatique. Similar pole/ fixture configurations that are taller and similar poles of the same height and design but with two or three heads seem to not be affected. Unfortunatley, Cooper excludes this from their warranty. Why they would allow this combination to be sold is uncertain to me and is a topic for a different forum. My question to readers that can identify with this problem is how did you ultimately resolve this? To what level did Cooper get involved. What pole did you replace with? Did you replace similar poles that showed no signs of cracking? How did you handle the warranty with the owner, general contractor, distributor and manufacturer? Is there anything I seem to be overlooking or not considering?
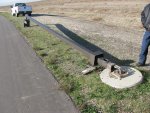
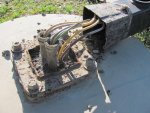
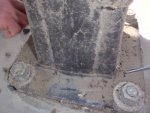