Stepper motor help (off topic... sorry ) an "Other Stuff" category would be nice
I would like to operate a component of a machine that contains a stepper motor on the test bench, for the puposes of adjustment and repair. I feel sure the OEM would frown upon this activity, so I don't think I could get much help from them.
I have an Oriental brand bipolar stepper motor with 4.5 ohms per winding. It is connected to a Sanken A2918SW motor driver. If anyone is interested the documentation is at :
www.allegromicro.com/en/products/categories/Sanken/Motor_Drivers/Motor_Driver_ICs_h1-i02eb0.pdf
There is not as much info on this model as others. I have disconnected the stepper driver board from the rest of the component, and am enabling and phasing it with a BASIC STAMP according to the truth table on the documentation. I think I have the sequence correct because I have tried all the combinations I can think of and this one seems to be the best.
The problem is it doesn't seem to have as much torque as it should.
VBB > Vref = 39VDC, and I am using enable ,1 enable 2, and phase 1, and phase 2 . It seems to me from looking at this drawing that I should have something hooked to E1 and E2, but I don't ... should I have something hooked to E1 and E2...any suggestions on the resistor values?
thanks
I would like to operate a component of a machine that contains a stepper motor on the test bench, for the puposes of adjustment and repair. I feel sure the OEM would frown upon this activity, so I don't think I could get much help from them.
I have an Oriental brand bipolar stepper motor with 4.5 ohms per winding. It is connected to a Sanken A2918SW motor driver. If anyone is interested the documentation is at :
www.allegromicro.com/en/products/categories/Sanken/Motor_Drivers/Motor_Driver_ICs_h1-i02eb0.pdf
There is not as much info on this model as others. I have disconnected the stepper driver board from the rest of the component, and am enabling and phasing it with a BASIC STAMP according to the truth table on the documentation. I think I have the sequence correct because I have tried all the combinations I can think of and this one seems to be the best.
The problem is it doesn't seem to have as much torque as it should.
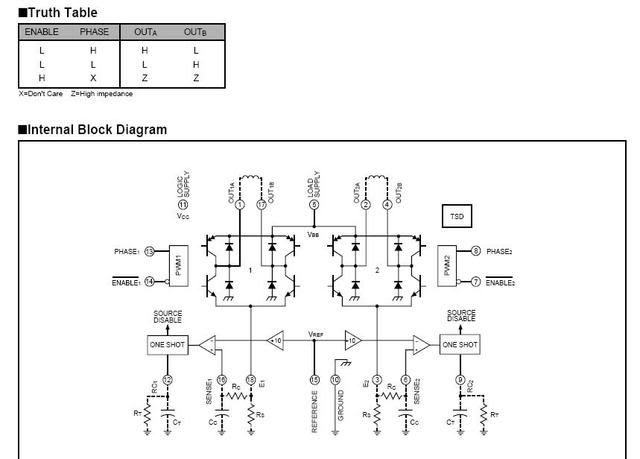
VBB > Vref = 39VDC, and I am using enable ,1 enable 2, and phase 1, and phase 2 . It seems to me from looking at this drawing that I should have something hooked to E1 and E2, but I don't ... should I have something hooked to E1 and E2...any suggestions on the resistor values?
thanks