I'm sure many others in this forum can relate to the squeeze that the parts shortage has been putting on many of us.
I'm faced with a situation where a 2 pole din rail mount breaker we have been using has become very hard to come by. I need several of these breakers for an application where we use 2 poles of a 3 phase 480v system to power a single phase device. Our supplier can get the 3 pole version of this breaker, which is physically the same dimensions. The only apparent difference is that unlike the 2 pole where the center position is empty, the 3 pole version allows connections to all 3 positions.
A much more experienced engineer that I work with, says that this can be done, however we should send one phase through the breaker twice (go through once, loop back up to the top of the breaker, and go through a second time on another pole) so that all 3 poles are occupied. I could see this maybe being done on a contactor where you are switching large inductive loads and want some additional protection from contacts welding, or an arc jumping the gap, but I don't see the benefit in our situation.
Is there any benefit to looping around to use all parts of the breaker? We already have several of the 2 pole breakers out in the field, and I would much rather wire the 3 pole breakers straight through so that our wiring is consistent throughout the project.
NEC and UL compliance is necessary.
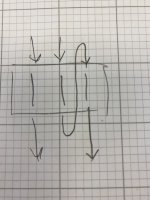
I'm faced with a situation where a 2 pole din rail mount breaker we have been using has become very hard to come by. I need several of these breakers for an application where we use 2 poles of a 3 phase 480v system to power a single phase device. Our supplier can get the 3 pole version of this breaker, which is physically the same dimensions. The only apparent difference is that unlike the 2 pole where the center position is empty, the 3 pole version allows connections to all 3 positions.
A much more experienced engineer that I work with, says that this can be done, however we should send one phase through the breaker twice (go through once, loop back up to the top of the breaker, and go through a second time on another pole) so that all 3 poles are occupied. I could see this maybe being done on a contactor where you are switching large inductive loads and want some additional protection from contacts welding, or an arc jumping the gap, but I don't see the benefit in our situation.
Is there any benefit to looping around to use all parts of the breaker? We already have several of the 2 pole breakers out in the field, and I would much rather wire the 3 pole breakers straight through so that our wiring is consistent throughout the project.
NEC and UL compliance is necessary.
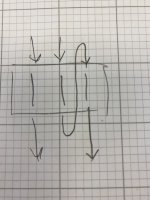