New to this industry. Not my job to size the equipment but from time to time I am required to come up with indicative pricing without proper engineering. I do not have an electrical degree but do have some knowledge. My questions are related to wire sizing related to parallel runs hooking up a Xfmr to an Inverter that connects to the battery storage containers. The example one line diagram below shows a Xfmr supplying 4 battery containers with nine 750kcmil conductors and one 350kcmil gnd conductor per each battery. It is my understanding that the gnd conductor must be sized to handle the same amp rating as the OCPD, but that doesnt seem to be the case here possibly due to derating which I am not that familiar with. Assuming 90deg CU with a size of 350kcmil the gnd can handle 350A. Yet with the battery having a 1,632kva rating (1,963FLA), I calculate nine 750kcmil conductors (3 parallel 3 phase runs) would only handle 1,605A (without derating). So, I am confused because it looks to me like 3 runs of 750kcmil is not adequate and neither is the single 350kcmil gnd conductor. I am also foggy on if these parallel runs are multi taps from a single CB or if each run has its own CB. Also, I am pretty sure going parallel isnt as simple as dividing the amps because you may only get 75-80% additionally ampacity on parallel runs. Some insight into this would be very much appreciated. Thank you
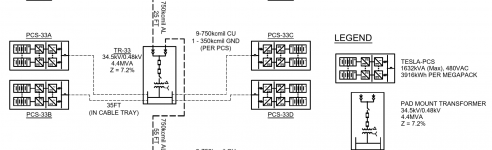
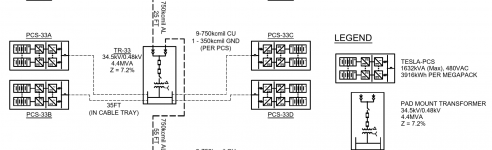