zbang
Senior Member
- Location
- Roughly 5346 miles from Earls Court
I've been doing some work on a friend's Coval surface grinder. It was built with a 3-phase motor to drive the worktable back and forth and does that using contactors (see below) There are no time delays involved, so when the reversing switch changes, one contactor falls out and the other comes on. Makes a racket and must be hard on the motor.... (There's also no speed control because someone so helpfully removed the variable-speed pulley and that's a $200+ part. No limit switches, either; probably removed long ago.)
We're thinking of ripping out the contactors and dropping in a handy 1.5HP Teco VFD to add some sanity to the whole thing. Assuming it's a Good Idea, what sort of accel/decel parameters should we use? Other parameters? I don't recall the ratio, but the existing motor-to-table-drive is maybe 75:1 and that really whips the table back and forth, so speed control is needed.
The existing motor, not original, is a 184 frame Dayton, 1.5HP 1150 rpm SF 1.0 208-220v. The parts list says the original was "Howell motor 3-ph 1/6HP 220/440v 60cy. A-66" which the manual says "is a special reversing motor and is expected to run hot" (I'd think it would, at least that's in the instructions).
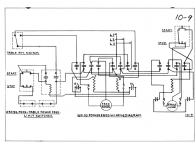
We're thinking of ripping out the contactors and dropping in a handy 1.5HP Teco VFD to add some sanity to the whole thing. Assuming it's a Good Idea, what sort of accel/decel parameters should we use? Other parameters? I don't recall the ratio, but the existing motor-to-table-drive is maybe 75:1 and that really whips the table back and forth, so speed control is needed.
The existing motor, not original, is a 184 frame Dayton, 1.5HP 1150 rpm SF 1.0 208-220v. The parts list says the original was "Howell motor 3-ph 1/6HP 220/440v 60cy. A-66" which the manual says "is a special reversing motor and is expected to run hot" (I'd think it would, at least that's in the instructions).
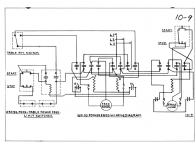