John Hawkinson
Member
- Location
- Cambridge, MA
- Occupation
- EECS (really CS — Computer Science. Not a PE.)
Hello. I hope this is a reasonable question to post here, it's been kicking around the back of my head for a long time, and I spent way too much time today trying to find an answer to no avail, although it's really just trivia.
Classically and historically, the screws to attach a device to a box were 6-32 flat head. And by "flat head" I mean true flat head screws with conical undersides and flat tops that are designed to sit flush in countersunk holes, I don't mean the straight "slotted" drive style (versus Phillips, Robertson, etc.), although device screws were usually that too. That is, style (e) in this diagram from Wikipedia:
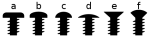
Nowadays, device screws that come with a receptacle are all 6-32 pan head (maybe extra-low profile compared to a normal pan head). That is, underside of the screw head is flat, and the top is slightly rounded. (Also they are Phillips. Or a variant like combination). Style (a) in the diagram [or maybe style (d)].
To the engineer in me, it's obvious that these screws should be pan head. The slot/hole in the yoke means that a flat head screw has just a line of contact with the device yoke; and since the hole is usually slotted, it's not even a full 360° of contact. Of course, a pan head screw has nearly the full surface area of the screw head in contact with the yoke, rather than the thin line (still, not 100% contact because of the slot, but still a lot more than the flat head).
And although modern receptacles now come with pan head screws, it appears that electrical prosumer manufacturers still seem to sell flat head screws in, e.g., screw kit assortments designed for devices (e.g. Gardner-Bender SK-632T; Southwire makes one too). Weirdly both market them as a "slotted flat head design" when they clearly use Phillips drive flat head screws (perhaps they did not used to and the marketing copy is old?).
Did outlet cover plates used to sit tighter against receptacles so there wasn't room for the added height of the pan head? When and why did it change?
I'm not sure if perhaps this is addressed in the NEMA OS 1, OS 2, or OS 3 standards (those are, respectively: Metallic Outlet Boxes; Nonmetallic Outlet Boxes, Device Boxes, Covers and Box Supports; and Selection and Installation Guidelines for Electrical Outlet Boxes), or maybe in their older versions?
Thanks for the history lesson!
Classically and historically, the screws to attach a device to a box were 6-32 flat head. And by "flat head" I mean true flat head screws with conical undersides and flat tops that are designed to sit flush in countersunk holes, I don't mean the straight "slotted" drive style (versus Phillips, Robertson, etc.), although device screws were usually that too. That is, style (e) in this diagram from Wikipedia:
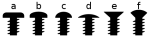
Nowadays, device screws that come with a receptacle are all 6-32 pan head (maybe extra-low profile compared to a normal pan head). That is, underside of the screw head is flat, and the top is slightly rounded. (Also they are Phillips. Or a variant like combination). Style (a) in the diagram [or maybe style (d)].
To the engineer in me, it's obvious that these screws should be pan head. The slot/hole in the yoke means that a flat head screw has just a line of contact with the device yoke; and since the hole is usually slotted, it's not even a full 360° of contact. Of course, a pan head screw has nearly the full surface area of the screw head in contact with the yoke, rather than the thin line (still, not 100% contact because of the slot, but still a lot more than the flat head).
And although modern receptacles now come with pan head screws, it appears that electrical prosumer manufacturers still seem to sell flat head screws in, e.g., screw kit assortments designed for devices (e.g. Gardner-Bender SK-632T; Southwire makes one too). Weirdly both market them as a "slotted flat head design" when they clearly use Phillips drive flat head screws (perhaps they did not used to and the marketing copy is old?).
Did outlet cover plates used to sit tighter against receptacles so there wasn't room for the added height of the pan head? When and why did it change?
I'm not sure if perhaps this is addressed in the NEMA OS 1, OS 2, or OS 3 standards (those are, respectively: Metallic Outlet Boxes; Nonmetallic Outlet Boxes, Device Boxes, Covers and Box Supports; and Selection and Installation Guidelines for Electrical Outlet Boxes), or maybe in their older versions?
Thanks for the history lesson!