I'm with Cow on this one.
Your disconnect guts need to be replaced.
We use Siemens disconnects almost exclusively and I've had to replace several of these over the years that have been fairly heavily loaded over a long period of time because they start generating too much heat at the switching mechanism which in turn starts to overheat the terminations and wiring. You got 6 years out of them since your original install. So now you know they have a 6 year lifespan in this environment, if you want longer service intervals, replace with 100 amp disconnects.
I do not believe strand count is playing a part in generating the heat. For instance, we do work for large farms with potato storages, typically 60 amp disconnects with 60 amp fuses to cords running as much potato piling equipment as they can plug in. Fuses blowing are common, but I do not see symptoms of overheating where the SO cords are ran right to the disconnect terminals.
I know fine stranded wire should not be terminated in this manner, but the reality is, generally it is not a problem.
The only terminations burning are the disconnect line side. Fine strand wiring type aside for the moment, no other connections are burning. Normally the heater end of the circuit would likely see the highest temperatures, and no issues mentioned there.
From your IR images its clear that the serious heat originates at the left two poles of the disconnect. At the bottom of the movable contact, and rising up from there.
In this image the right pole is not as hot, and has a better connection. The first two poles running at 87C, is well over the 75C terminal rating, and real close to the 90C wire maximum rating. The rotating bar contacts are not making a good connection with the stationary contacts. This is likely where you will read the most FOP.
Where I differ with Cow is I would not replace the guts, I would replace with a better designed switch. A 6 year lifespan for industrial equipment is way too short, for my liking. I do not use rotating bar type disconnects on my projects after seeing them fail after thirty days from the install, for this same reason. Poor connection from the single sided wiping contact connections. Often they do not fully mechanically engage when turned on. GE was another adopter of this style mechanism early on. They work OK on commercial work, but not for continuous industrial loads, that are run near their rating.
The plasticizer oil is being baked out of the wire insulation, running down the switch internals and rear wall and accumulating on the bottom. Remove the arc chute and look at the rotating contact bars, they look heavily oxidized as compared to the stationary contact plating from the photo.
Cleaning and lubing the contacts, will not correct for the spring tension lost in the tempered, side pressure contact spring. I prefer switches that have a knife blade construction or vacu break contacts. Knife blade types have two connection points on each end of the movable blade, and spring pressure on each side. Sq D is one of the makers of a HD knife blade construction, as do others.
Meanwhile the breaker termination seems to be surviving fine at 44C, looks as if the bottom pole is a tad cooler, like the right pole in the switch, better contact connection in the rotary switch.
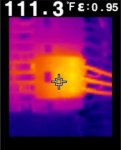