shockking
Member
- Location
- Sacramento, CA
- Occupation
- engineer
Does phase rotation matter for this SCR? Diagrams below.
Context: We have a 1,000 HP motor originally installed in 1987. It gets DC power from a three-phase silicon controlled rectifier (SCR) bridge rectifier assembly. I'm not too familiar with these so I'm doing some reading. I'm trying to confirm if phase rotation matters for this circuit. We replaced the step down transformer and we're trying to tell if it will be a problem if for some reason the phase rotation gets reversed. The documentation describes a phase sensing circuit on the firing circuit board. But I can't tell if this is sensing rotation, or what exactly.
Here's the rectifier diagram:
Detail of the hard firing circuit:
Schematic of the firing circuit board and regulator board:
Thanks in advance for any advice.
Context: We have a 1,000 HP motor originally installed in 1987. It gets DC power from a three-phase silicon controlled rectifier (SCR) bridge rectifier assembly. I'm not too familiar with these so I'm doing some reading. I'm trying to confirm if phase rotation matters for this circuit. We replaced the step down transformer and we're trying to tell if it will be a problem if for some reason the phase rotation gets reversed. The documentation describes a phase sensing circuit on the firing circuit board. But I can't tell if this is sensing rotation, or what exactly.
Here's the rectifier diagram:
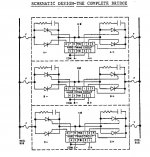
Detail of the hard firing circuit:
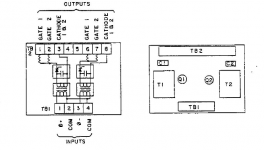
Schematic of the firing circuit board and regulator board:
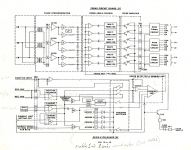
Thanks in advance for any advice.