mgookin
Senior Member
- Location
- Fort Myers, FL
- Occupation
- Retired inspector, plans examiner & building official
I read some older threads on this forum about landing stranded wire on screw terminals such as receptacles and switches. It appears to be allowed and there were some good tips mentioned:
1. Twist the wire CCW so it pulls together vs. pushing apart as the screw is tightened.
2. Tinning the wire. We already do that anyway even if landing in a wirenut to a solid conductor; it just makes better looking work. We tell our people to expect that every unit has the same chance of landing in a testing lab and if it's not good enough for that, it doesn't go out.
The discussion thread on this subject was from 2011. Does anyone have any information to indicate whether there have been any changes with respect to this being allowed?
I just did some experimenting after reading the thread. On one I left it with the factory CW twist and the other I twisted CCW. I found that the CCW twist became a larger diameter because I am unable to twist it as tightly and neatly as is done in the wire factory.
On both of them I formed the lead by wrapping around a rod, then tinned the lead.
As you can see, the CCW is a poorer job with wire protruding from under the screw. Not only was it harder to get under the screw head because of larger diameter, it was also hard to keep it from being pushed out as I tightened the screw. With a smaller diameter wire the results would probably be different but for now I'm sticking with CW twist.
Here's what I got:
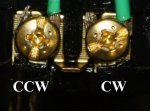
1. Twist the wire CCW so it pulls together vs. pushing apart as the screw is tightened.
2. Tinning the wire. We already do that anyway even if landing in a wirenut to a solid conductor; it just makes better looking work. We tell our people to expect that every unit has the same chance of landing in a testing lab and if it's not good enough for that, it doesn't go out.
The discussion thread on this subject was from 2011. Does anyone have any information to indicate whether there have been any changes with respect to this being allowed?
I just did some experimenting after reading the thread. On one I left it with the factory CW twist and the other I twisted CCW. I found that the CCW twist became a larger diameter because I am unable to twist it as tightly and neatly as is done in the wire factory.
On both of them I formed the lead by wrapping around a rod, then tinned the lead.
As you can see, the CCW is a poorer job with wire protruding from under the screw. Not only was it harder to get under the screw head because of larger diameter, it was also hard to keep it from being pushed out as I tightened the screw. With a smaller diameter wire the results would probably be different but for now I'm sticking with CW twist.
Here's what I got:
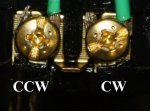